
TLT-COMPOSITE
Your trusted composite technology partner
TLT-Composite is your composite technology partner for product development
from the product development phase to component delivery and every step in between!
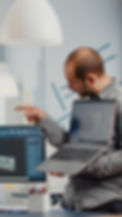
PRODUCT DEVELOPMENT
Product development is the most critical stage of the product cost structure and requires good collaboration with the customer from an early stage.
CLOSE COOPERATION
A significant part of the cost of a new product is determined at the product development stage. This phase is particularly important for composite materials as there are many alternatives, material combinations and manufacturing processes to choose from.
Good choices made in the product development phase have a significant impact on the manufacturing costs in the mass production phase. Our experience has shown that the best results are achieved by the customer's knowledge of the most appropriate materials and manufacturing technology, and by very close cooperation with an innovative product development team with experience and knowledge.
The first step in controlling product costs is to understand the requirements of the manufacturing process and the desired manufacturing technologies. As our customers know their own products best, we work with them at the definition stage to define as thoroughly and clearly as possible the requirements and expectations of the product.
THE VIRTUAL MODELS
During product development, we create 3D models of the products, allowing early analysis of manufacturing and raw material alternatives and cost comparisons. 3D models can also act as an illustrative communication tool when discussing issues such as how the product relates to the rest of the structure or its appearance, or even its load-bearing capacity.
In addition to virtual models, we can also produce physical models, sub-assemblies and test pieces as required to help our customers in their decision-making. We use cost-effective tools and manufacturing processes to minimise costs during the product development phase.
DESIGN, ANALYSIS AND TOOLING
GOOD DESIGN KEEPS CARBON FIBRE PRODUCT PRICES COMPETITIVE
Designing composite pieces requires knowledge of the properties of the materials and the possibilities offered by different manufacturing techniques. We have extensive experience in designing a wide range of composite parts from small parts to large machine parts to meet extreme requirements.
Product design starts with a pre-engineering phase that allows the definition of important product properties such as manufacturing cost, weight and stiffness. This supports decision-making when considering different composite materials for a new product.
For products, we carry out manufacturing technology and tool design. This ensures good tool and mould functionality in our manufacturing processes, which translates into competitive composite product prices.
CARBON FIBRE COMPOSITES
In load-bearing structures, carbon fibre composites offer weight savings of more than 50 percent compared to steel and 30-40 percent compared to aluminium.
The strength and stiffness of a carbon fibre composite structure are carefully optimised according to the load.
The product can be subject to small, negligible or negative thermal expansion.
Carbon fibre allows for more creative and impressive designs than conventional materials.
The degree of integration can be increased: the fewer carbon fibre components and assemblies, the fewer tolerance problems.
The structures can be combined with a variety of materials and components: other composites, metals, inserts, threaded parts, etc...
Composite materials allow new sizing criteria: up to twice the elongation of steel and aluminium.
Composite parts can achieve almost unlimited resistance to vibration and fatigue.


OUR PRODUCTION METHODS
Vacuum technology, vacuum injection and various pressing processes, manual lamination, allow us to produce composite products with extremely uniform quality and excellent surface finish.
Parts produced by the above mentioned processes are quite often combined with composite parts. We deliver the products to our customers in the required format as components, assembled or fitted.